Spars & Oars
We have both worked on and built a number of spars and oars. Dani has built a new 14’ solid Sitka Spruce mast for a sailing dinghy, built a hollow ‘birdsmouth’ spar for a RNSA sailing dinghy, worked on a solid 80’ Douglas Fir mast that needed significant rot removal, and has made a handful of spooned oars. Sam has worked on many of the Salcombe Yawl masts from the fleet, repaired numerous gig oars and together we have worked on the wooden mizzen mast from our own boat.

Top view of hollow birdsmouth mast

recessed notches for thumb cleats on hollow spar

adding a tapered block to a hollow mast

Making wooden oars

Making wooden oars

Shaping an oar

Oar after oiling

Curved blades to the oars

Sapele highlights through the blades
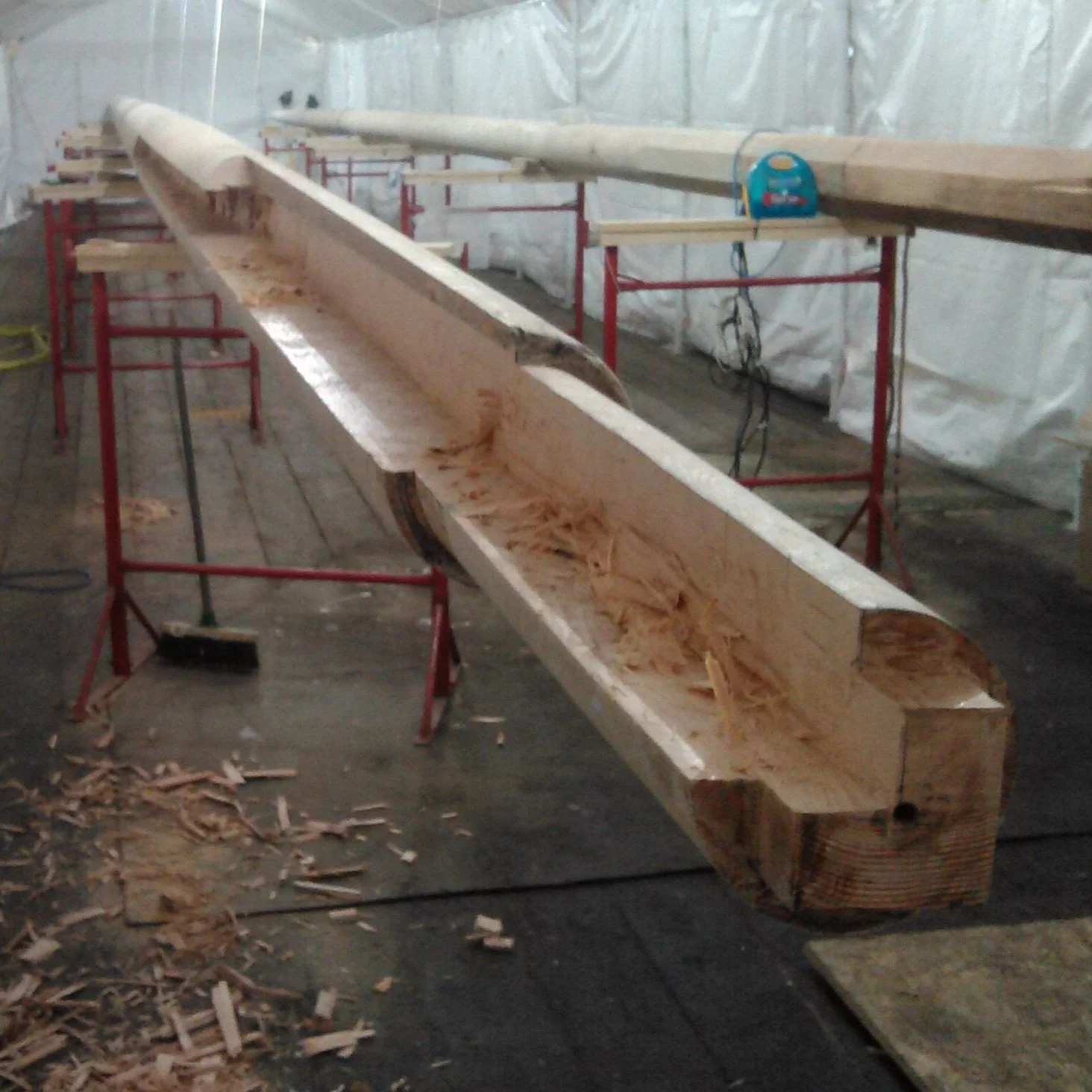
Rot finding and removal on 80' mast from a Sail Training Vessel

Gluing up a 14' piece of Sitka Spruce to make a sailing dinghy mast

The glued mast, marking up to take it from square to octagonal.

Knocking the corners off

Halfway from square to octoganal

Fully octagonal

Marking up to make the mast 16-sided

Marking up to make the mast 16-sided

16 sided

Smoothing by eye to round the mast

Marking up a square tenon

Rough cut square tenon

Cutting a round tenon on the other end of the mast

Knocking off corners to octagonal for the tenon

octagonal tenon, then marked up for 16 siding

16-sided tenon, then rounded by eye

We found rot in the top section of our mizzen

We cut the top, and marked the scarf length
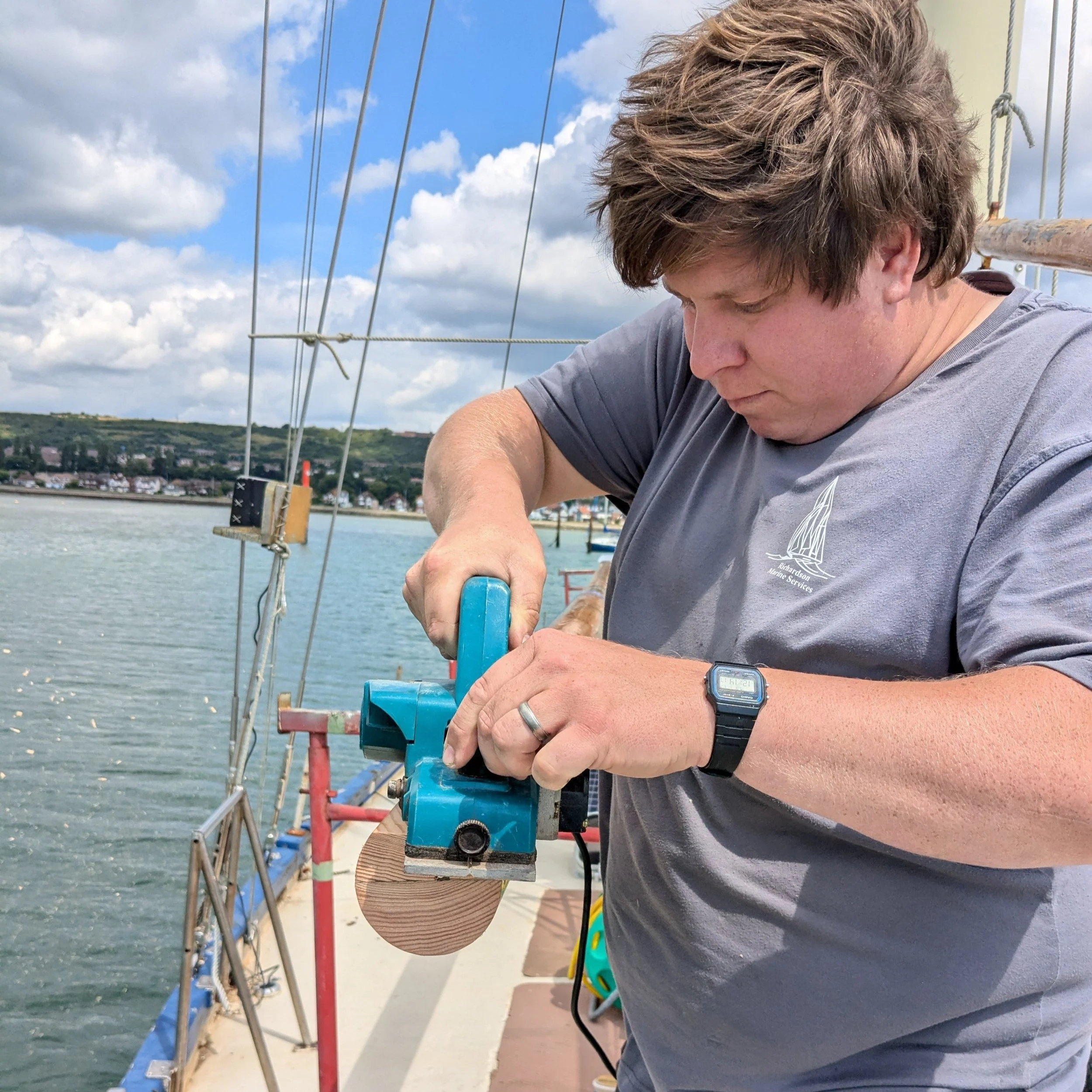
We planed the mast down to a point

This is a 12:1 ratio, for scarf joints on spars

New top mast sections laminated together

Mapping out the matching scarf joint

Planing them to match our mast

Here they areglued together
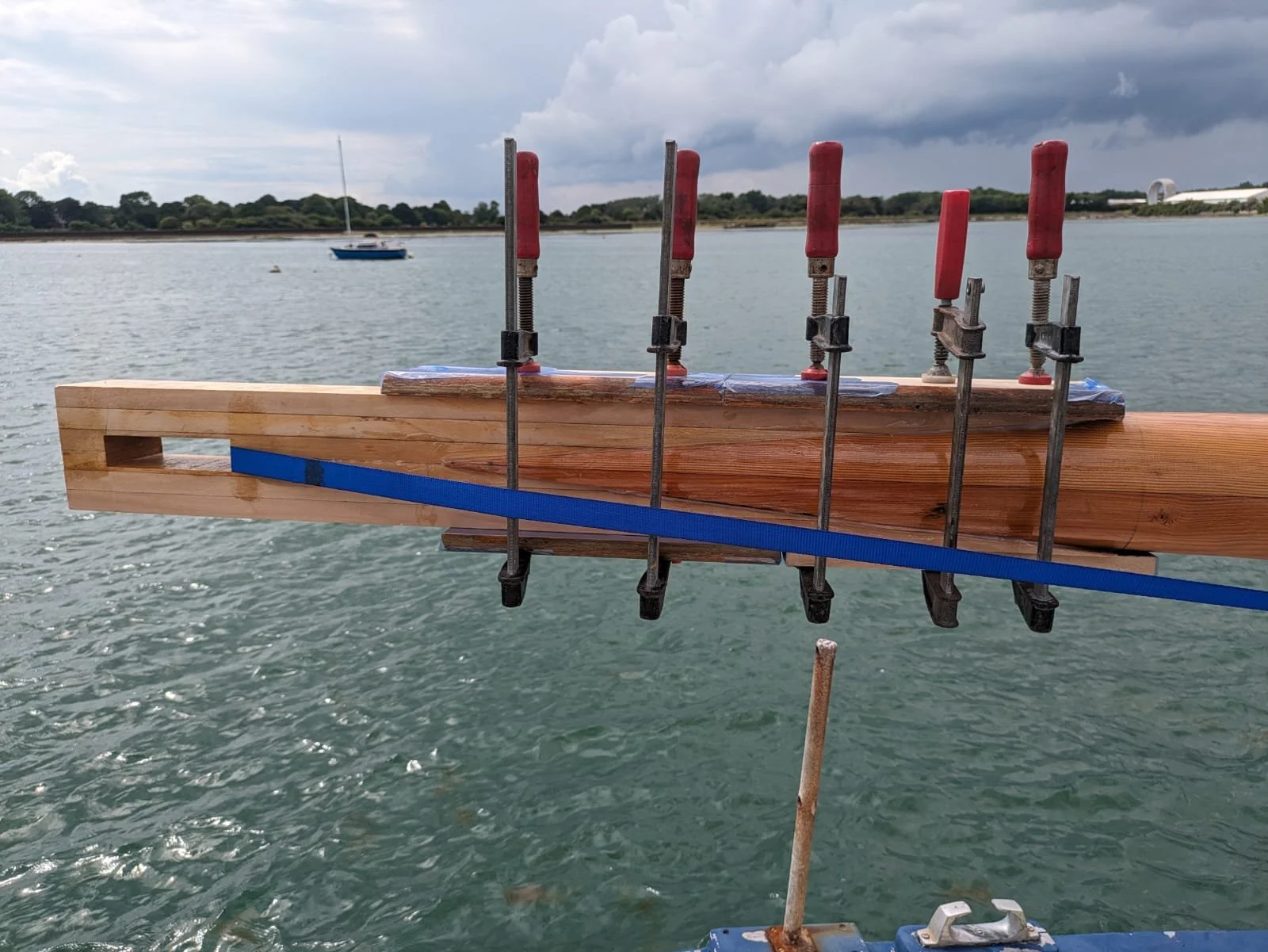
New top mast glued to our old mast

After shaping the first lamination we added extra cheeks to match the repair to the original thickness. This was a necessary step because we wanted to use reclaimed timber and the mast we had wasn't the same size as ours.

And then we shaped the extra cheeks in too